Corten Corrugated Panels A Comprehensive Guide
Corten corrugated panels offer a compelling aesthetic and durability for various construction projects. This guide delves into their diverse applications, exploring their suitability for residential, commercial, and industrial settings. We’ll examine successful project examples, compare them to other materials, and discuss the environmental impact of their use.
From material properties and manufacturing processes to installation and maintenance, this comprehensive resource provides detailed information. Understanding the unique characteristics of corten steel, the various finishes available, and their resistance to corrosion and weathering in different climates is crucial for effective use.
Material Properties and Features
Corten steel, renowned for its unique weathering properties, is an ideal material for corrugated panels. Its ability to develop a protective rust-like patina, which acts as a barrier against further corrosion, makes it remarkably durable and resilient to the elements. This inherent characteristic allows for long-term outdoor applications without the need for extensive maintenance.
The inherent properties of corten steel, particularly its high tensile strength and exceptional resistance to atmospheric corrosion, make it a superior choice for structural elements like corrugated panels. This robust material is designed to withstand various environmental stresses, making it suitable for diverse applications, from residential roofing to industrial structures.
Unique Properties of Corten Steel
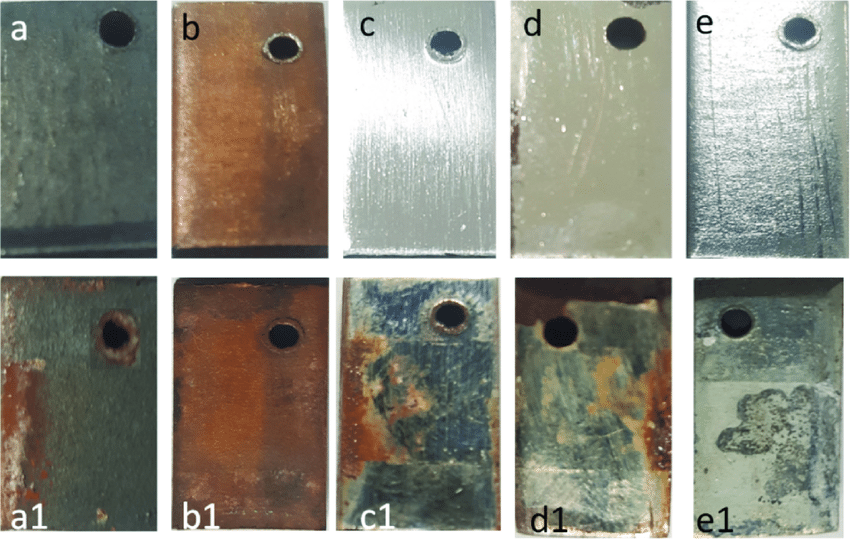
Corten steel’s exceptional durability stems from its unique chemical composition. Specifically, the alloying elements, such as chromium, copper, and phosphorus, promote the formation of a protective layer of rust. This layer, known as a patina, is not merely rust but a tightly adherent, corrosion-resistant oxide layer. This self-healing characteristic ensures ongoing protection against further corrosion, even after initial exposure.
Manufacturing Process of Corten Corrugated Panels
The manufacturing process for corten corrugated panels typically involves several stages, ensuring consistent quality and structural integrity. First, high-quality corten steel coils are procured. These coils are then fed into a specialized corrugating machine. The machine precisely shapes the steel into the desired corrugated profile. Subsequent steps include cutting the panels to the required dimensions and ensuring that the panels meet predetermined quality standards. Rigorous quality control measures are implemented at each stage of production to guarantee dimensional accuracy, material consistency, and structural integrity. These checks include visual inspections, dimensional measurements, and mechanical testing to verify strength and stability.
Advantages and Disadvantages Compared to Other Steel Types
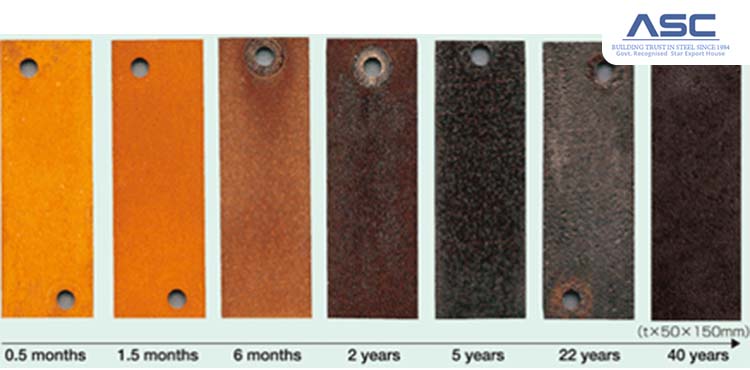
Corten steel, while highly durable, has advantages and disadvantages compared to other steel types. Advantages include its exceptional resistance to weathering and corrosion, leading to minimal maintenance requirements. Disadvantages include a higher initial cost compared to some other steel types, and the distinctive reddish-brown appearance that some may find less aesthetically pleasing.
Available Finishes and Surface Treatments
Various finishes and surface treatments are available for corten corrugated panels, each impacting both visual appeal and longevity.
Finish | Appearance | Durability | Cost |
---|---|---|---|
Bare Corten | Distinctive reddish-brown patina | High, self-healing | Moderate |
Pre-painted Corten | A variety of colors | Very High, additional protection | High |
Powder Coated Corten | Wide range of colors and finishes | Excellent, enhanced protection | High |
Galvanized Corten | Zinc coating | High, additional corrosion protection | Moderate to High |
The choice of finish directly influences the panel’s aesthetic and long-term performance. Pre-painted or powder-coated options offer enhanced durability and a wider range of color choices, but come with a higher cost.
Corrosion and Weathering Resistance in Various Climates
Corten steel’s inherent corrosion resistance is significantly enhanced by the formation of a protective patina. This patina’s effectiveness in mitigating corrosion varies depending on the local climate. In climates with high humidity and frequent rainfall, the patina develops more rapidly and effectively, providing superior protection. In arid climates, the patina formation rate may be slower, but the inherent corrosion resistance still offers significant protection. Real-world examples of corten steel structures in diverse climates consistently demonstrate their remarkable resilience and longevity.
Installation and Maintenance: Corten Corrugated Panels
Corten corrugated panels, renowned for their aesthetic appeal and durability, demand meticulous installation and ongoing maintenance for optimal performance. Proper installation ensures structural integrity and longevity, while diligent maintenance preserves the panels’ unique aesthetic and protects against deterioration. This section details the critical steps and considerations for both installation and maintenance.
Installation Procedures
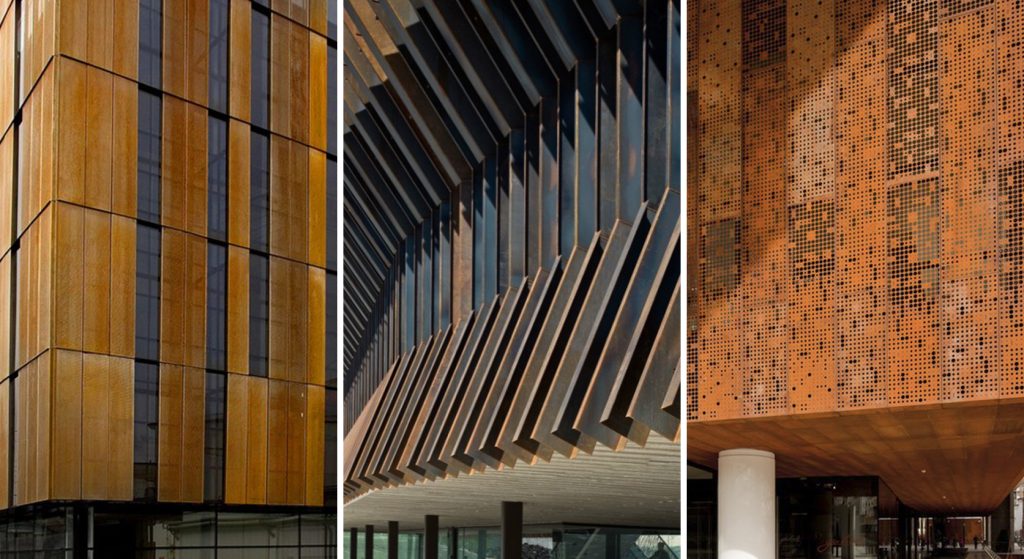
Careful planning and execution are paramount during installation. The support system significantly influences the panel’s structural performance. A robust framework, designed to withstand anticipated loads and environmental stresses, is essential. This includes consideration of wind loads, snow accumulation, and potential seismic activity, depending on the project location.
- Foundation Preparation: Thorough site preparation is crucial. Ensure a level and stable foundation to prevent uneven settling and panel distortion. Use appropriate leveling tools to establish the required precision. This initial step directly impacts the structural integrity of the final installation.
- Support System Design: The support system must be engineered to accommodate the weight and span of the corrugated panels. Properly spaced and securely anchored support structures, such as beams or posts, are vital. Consult structural engineering guidelines to ensure the structural adequacy of the chosen support system.
- Panel Alignment and Connection: Precise alignment of the panels is crucial for a seamless and aesthetically pleasing finish. Employ appropriate tools and techniques to maintain accurate alignment throughout the installation process. Securing the panels using suitable fasteners, like rivets or screws, is critical to ensure long-term structural integrity.
- Fastening Techniques: Proper fastening techniques are critical to prevent panel movement and maintain structural integrity. Use appropriate fasteners, ensuring they are adequate for the panel material and intended load. Avoid over-tightening, which can damage the panels. Follow the manufacturer’s specifications for fastener types and spacing.
Securing and Fastening
Effective fastening methods are vital for preventing panel movement, guaranteeing long-term performance, and maintaining the aesthetic integrity of the structure.
- Fastener Selection: Select fasteners appropriate for the panel material, considering factors such as corrosion resistance and load capacity. Choose fasteners that are compatible with the panel’s corrugations and prevent damage during installation.
- Fastener Spacing: Appropriate spacing of fasteners is crucial. Insufficient spacing can compromise the panel’s structural integrity, while excessive spacing can lead to gaps and visual imperfections. Consult the manufacturer’s recommendations for optimal spacing.
- Sealant Application: Sealant application, where appropriate, is important to prevent water ingress and ensure the long-term performance of the structure. Apply sealant around panel joints and edges to provide an additional barrier against water penetration.
Maintenance Procedures, Corten corrugated panels
Regular maintenance helps preserve the aesthetic appeal and integrity of corten corrugated panels.
- Cleaning: Regular cleaning is necessary to remove accumulated dirt, debris, and other contaminants. Mild detergent solutions, or even pressure washing (with caution), can be used to remove dust and dirt, preserving the panel’s surface and aesthetic appeal. Avoid harsh chemicals that could damage the panel’s protective oxide layer.
- Corrosion Monitoring: Inspect panels regularly for signs of corrosion. Early detection and addressing of corrosion issues can prevent significant damage and maintain the structural integrity of the panel. This is particularly important in high-humidity or salt-laden environments.
- Repairing Damage: Promptly address any visible damage to the panels. Minor scratches or dents can be repaired using appropriate patching materials or techniques. Major damage may necessitate replacement. Be cautious when dealing with potential damage, as neglecting these could lead to structural weakening over time.
Tools and Equipment
The following tools and equipment are typically required for installation and maintenance:
Category | Tools/Equipment |
---|---|
Installation | Level, measuring tape, safety harness, drill, fasteners, hammer, etc. |
Maintenance | Cleaning solutions, pressure washer (optional), protective gear, inspection tools, etc. |
Challenges in Different Architectural Contexts
Installation and maintenance challenges vary based on the architectural context.
- High-wind areas: Strong winds can exert significant forces on the panels. The design must account for these forces to ensure structural integrity and safety.
- Coastal environments: Coastal areas are often subjected to salt spray and high humidity, accelerating corrosion. Choosing corrosion-resistant materials and implementing protective measures is essential in these environments.
- Rooftop applications: Rooftop installations require careful consideration of load-bearing capacities and water drainage. Adequate support systems and proper drainage are crucial.
Outcome Summary
Source: alicdn.com
In conclusion, corten corrugated panels present a compelling alternative for roofing and cladding applications. Their durability, aesthetic appeal, and cost-effectiveness, along with their environmental friendliness, make them a versatile solution for a wide range of projects. The detailed insights into material properties, installation procedures, and maintenance strategies empower users to make informed decisions and maximize the lifespan of these panels. By understanding the challenges associated with installation and maintenance in diverse architectural contexts, project managers can confidently integrate corten corrugated panels into their designs.