Corrugated Corten Steel Panels A Comprehensive Guide
Corrugated corten steel panels offer a compelling blend of aesthetic appeal and practical benefits. From industrial exteriors to rustic agricultural structures, these panels are proving themselves adaptable to a wide range of applications. Their unique rust-colored patina adds a touch of character, while their durability makes them a cost-effective and reliable choice. This guide explores the multifaceted world of corrugated corten steel panels, from their diverse applications and manufacturing processes to crucial design and installation considerations.
This exploration delves into the various industries where corrugated corten steel panels excel, showcasing examples of their successful implementation in architectural and design projects. We’ll examine the manufacturing process, outlining the steps involved in creating these panels, from initial steel sheet preparation to final finishing touches. Furthermore, critical design considerations, including panel sizing and installation methods, are thoroughly discussed to ensure optimal results.
Corrugated Corten Steel Panel Applications
Corrugated Corten steel panels, renowned for their unique aesthetic and durability, are increasingly popular across various industries. Their inherent rust-prevention characteristics and adaptable design allow for a wide range of applications, from simple fencing to complex architectural facades. This exploration delves into the diverse uses of these panels, showcasing their versatility and the specific benefits they offer in different contexts.
Industries Utilizing Corrugated Corten Steel Panels
Corrugated Corten steel panels are finding applications in numerous industries, primarily due to their robust construction and visually appealing nature. Their ability to withstand harsh weather conditions and exhibit a distinctive patina further enhances their suitability for diverse projects.
Industry | Application | Benefits | Aesthetic Considerations |
---|---|---|---|
Construction | Exterior cladding, roofing, fencing, and wall panels | Exceptional durability and weather resistance, long lifespan, aesthetic appeal, fire resistance, and cost-effectiveness compared to other materials like aluminum or stainless steel. | Creates a modern, industrial, and rugged aesthetic. The panels’ unique patina, or natural rusting, adds character and visual interest to buildings, creating a dynamic look that evolves. |
Agriculture | Fencing, farm sheds, barns, and animal shelters | Rust resistance, affordability, ease of installation, high strength-to-weight ratio, and durability in harsh weather conditions. | Provides a rustic and durable aesthetic, blending well with the surrounding environment. The panels’ rugged appearance is often desired in agricultural settings, contributing to the overall aesthetic of the farm. |
Industrial | Warehouses, storage facilities, and industrial sheds | Cost-effectiveness, durability, and the ability to withstand heavy-duty applications, resistance to extreme temperatures. | Adds a modern, industrial feel to industrial structures, enhancing their aesthetic appeal while maintaining practicality. |
Transportation | Railroad cars, train stations, and other infrastructure elements | Strength, durability, ability to withstand environmental stressors, and corrosion resistance. | Creates a distinctive and visually striking aesthetic that can be tailored to the overall design of transportation infrastructure. |
Architectural Design | Facades, walls, and roofs of contemporary structures | Unique aesthetic qualities, flexibility in design, and the ability to be customized for a variety of architectural styles. | Provides a striking and distinctive aesthetic, often seen in modern or industrial architectural projects. The panels’ natural aging process adds a dynamic quality to the design. |
Examples of Unique Architectural Projects
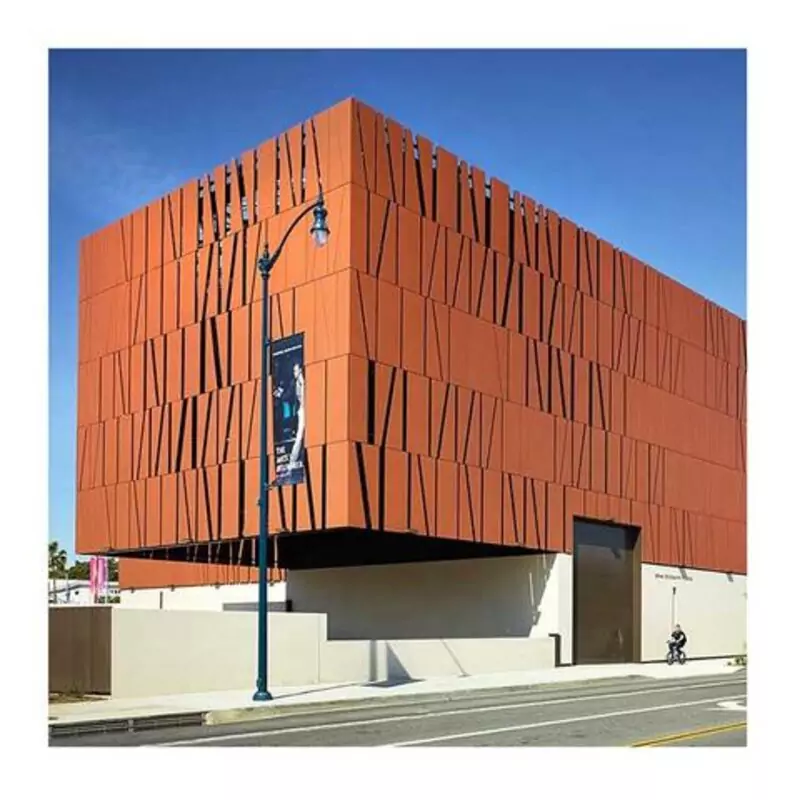
Several noteworthy architectural projects have successfully incorporated corrugated Corten steel panels. These panels have been used in a variety of contexts, showcasing their design versatility.
- The renovation of a historic warehouse in Chicago used corrugated Corten steel panels to create a modern, industrial aesthetic while respecting the building’s historical context. The panels were strategically placed to emphasize both the building’s past and its contemporary adaptation.
- A contemporary art museum in New York City featured an exterior wall clad in corrugated Corten steel panels. The panels’ evolving patina was a key design element, reflecting the museum’s focus on the passage of time and the beauty of natural processes.
- A sustainable farm complex incorporated corrugated Corten steel panels for fencing and sheds. The panels’ durability and rust resistance were essential for withstanding the harsh agricultural environment, while their rustic aesthetic seamlessly integrated with the surrounding landscape.
Aesthetic Qualities and Benefits
Corrugated Corten steel panels offer a distinctive aesthetic that sets them apart from other materials. Their inherent ability to develop a unique, natural patina over time provides a dynamic and ever-changing visual appeal.
- Distinctive Patina: The rusting process creates a visually appealing and evolving patina that distinguishes Corten steel from other materials. This natural aging effect adds character and depth to any structure.
- Modern Industrial Aesthetics: The corrugated design and the natural weathering give the panels a strong, industrial aesthetic, suitable for a range of architectural styles.
- Durability and Longevity: The rust-resistant properties of Corten steel make it a durable material that requires minimal maintenance over time, offering a long lifespan.
Manufacturing and Fabrication Processes
Corrugated Corten steel panels undergo a series of carefully controlled processes to achieve their final form and quality. These processes ensure the panels meet the required structural integrity, aesthetic appeal, and resistance to environmental factors. Understanding these manufacturing methods is crucial for appreciating the complexity and precision involved in producing these panels.
Steel Sheet Preparation
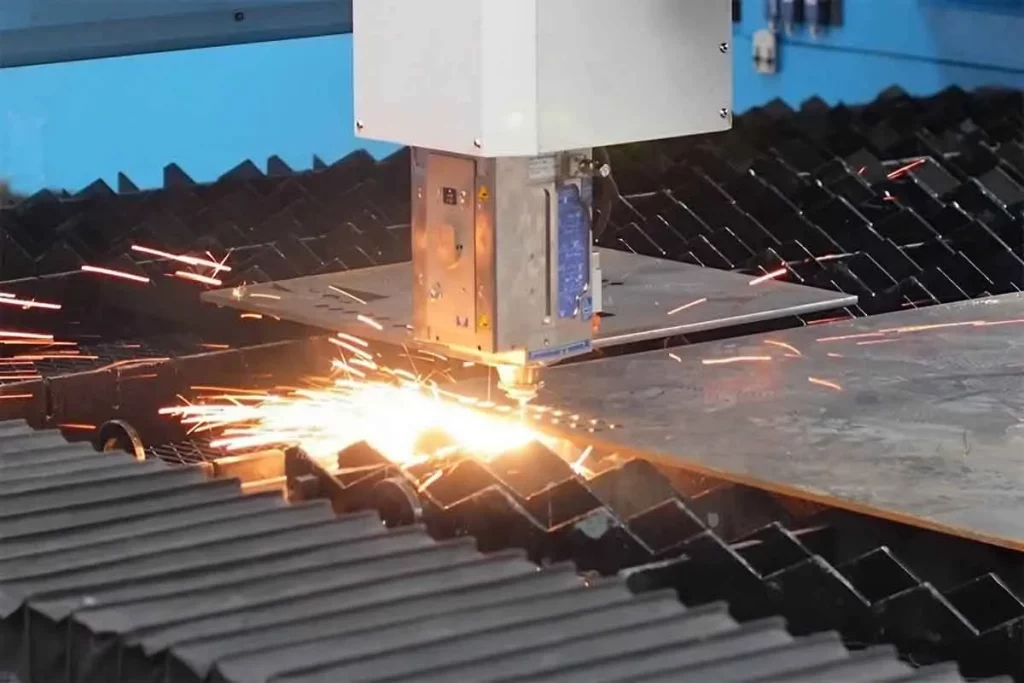
The initial stage involves meticulous preparation of the Corten steel sheets. Precise cutting and shearing techniques are employed to achieve the desired dimensions for the panels. These operations ensure the sheets are uniform in size and thickness, laying the groundwork for the subsequent corrugation process. Accurate measurements and tolerances are essential to guarantee the panels meet the specifications for intended use.
Corrugation, Corrugated corten steel panels
The corrugation process is a crucial step in shaping the panels. Specialized rolling machines apply controlled pressure to the steel sheets, creating the characteristic corrugated texture. The rolling process involves a precise combination of force and speed to achieve the desired depth and pitch of the corrugations. The type of rolling machine used significantly affects the panel’s final aesthetic.
Finishing
Protective coatings are vital to the longevity and aesthetic appeal of the corrugated Corten steel panels. Methods such as painting and powder coating are commonly used. Painting typically involves multiple coats of specialized paints designed to resist corrosion and weathering. Powder coating, a more advanced technique, involves applying a fine powder to the panel, which is then cured through a heating process. The choice of finishing method depends on the specific project requirements and desired level of protection.
Welding, Cutting, and Other Techniques
Welding plays a crucial role in assembling the panels, especially for larger structures or those requiring greater structural integrity. Various welding techniques are employed depending on the project’s needs. Cutting techniques are essential for achieving intricate shapes and designs, while other fabrication methods may be necessary for specific applications. The precision of these processes ensures the structural integrity and longevity of the panels.
Manufacturing Process Steps
Step | Description | Materials | Techniques |
---|---|---|---|
1 | Steel sheet preparation: Cutting and shearing to achieve the desired dimensions for the panels. | Corten steel sheets | Cutting, shearing, and measuring |
2 | Corrugation: Applying controlled pressure to the steel sheets to create the corrugated texture. | Corten steel sheets | Rolling, forming |
3 | Finishing: Applying protective coatings to resist corrosion and weathering. | Protective coatings (paint, powder) | Painting, powder coating |
4 | Welding (if required): Joining panels for larger structures. | Corten steel | Various welding techniques (e.g., MIG, TIG) |
5 | Cutting (if required): Achieving intricate shapes and designs. | Corten steel | Various cutting techniques (e.g., plasma, laser) |
Design Considerations and Considerations for Installation
Source: art-metal.ca
Corrugated Corten steel panels, with their distinctive aesthetic and durability, offer a versatile solution for various architectural projects. Careful design and installation are crucial to realizing the full potential of these panels, ensuring both their structural integrity and aesthetic appeal. Understanding the specific factors influencing their application is vital.
Designing with corrugated Corten steel panels requires a thoughtful approach. Consideration must be given to the panel’s inherent characteristics, including its weight, the strength of the corrugations, and its dimensional stability. These factors, along with the chosen installation methods, dictate the panel’s overall performance and longevity.
Structural Considerations for Supporting and Fixing Panels
The structural design of the supporting framework plays a critical role in the longevity and safety of the entire structure. Adequate support is paramount to withstand anticipated loads, including wind, snow, and potential seismic activity. Engineers must account for the panel’s weight and the distribution of that weight across the supporting structure. The design should ensure that the supporting elements can handle the load without compromising structural integrity.
Proper fixing methods are equally critical. Choosing appropriate fasteners, such as bolts or specialized clips, is essential. The selection should take into account the panel material, the supporting structure, and the specific environmental conditions. For instance, in areas with high humidity or corrosive environments, corrosion-resistant fasteners are necessary. This approach will extend the life of the entire system.
Methods and Procedures for Proper Installation
Thorough planning and meticulous execution are crucial for a successful installation. This process involves precise measurements, careful alignment, and secure fastening of the panels. The correct application of these methods minimizes the risk of damage or failure.
- Panel Alignment: Precise alignment of the panels is critical for maintaining the aesthetic integrity of the structure. Careful measurements and use of specialized tools are essential to ensure that the panels are correctly positioned and aligned with each other.
- Fastening Techniques: Selection of appropriate fasteners is vital for ensuring the panels are securely fastened to the supporting structure. Bolting, welding, or specialized fastening systems are used depending on the panel size, the structure, and the specific project requirements.
- Sealant Application: Proper sealant application is essential to prevent water ingress and protect the panels from corrosion. Choosing the right sealant type, considering the environment, is critical for long-term performance.
Comparison of Panel Sizes and Suitability
Different panel sizes offer distinct advantages and disadvantages, making them suitable for various projects.
Panel Size | Suitability | Installation Method | Advantages |
---|---|---|---|
Large | Large-scale projects, such as facades of large buildings or expansive walls. | Bolting, welding | Stronger, more robust structure, fewer joints, reduced labor cost for large projects. |
Small | Detailed designs, intricate geometries, and smaller projects. | Fastening systems, such as clips or specialized fasteners. | More adaptable to complex geometries, easier to work with in tight spaces, and reduced material waste. |
Final Summary: Corrugated Corten Steel Panels
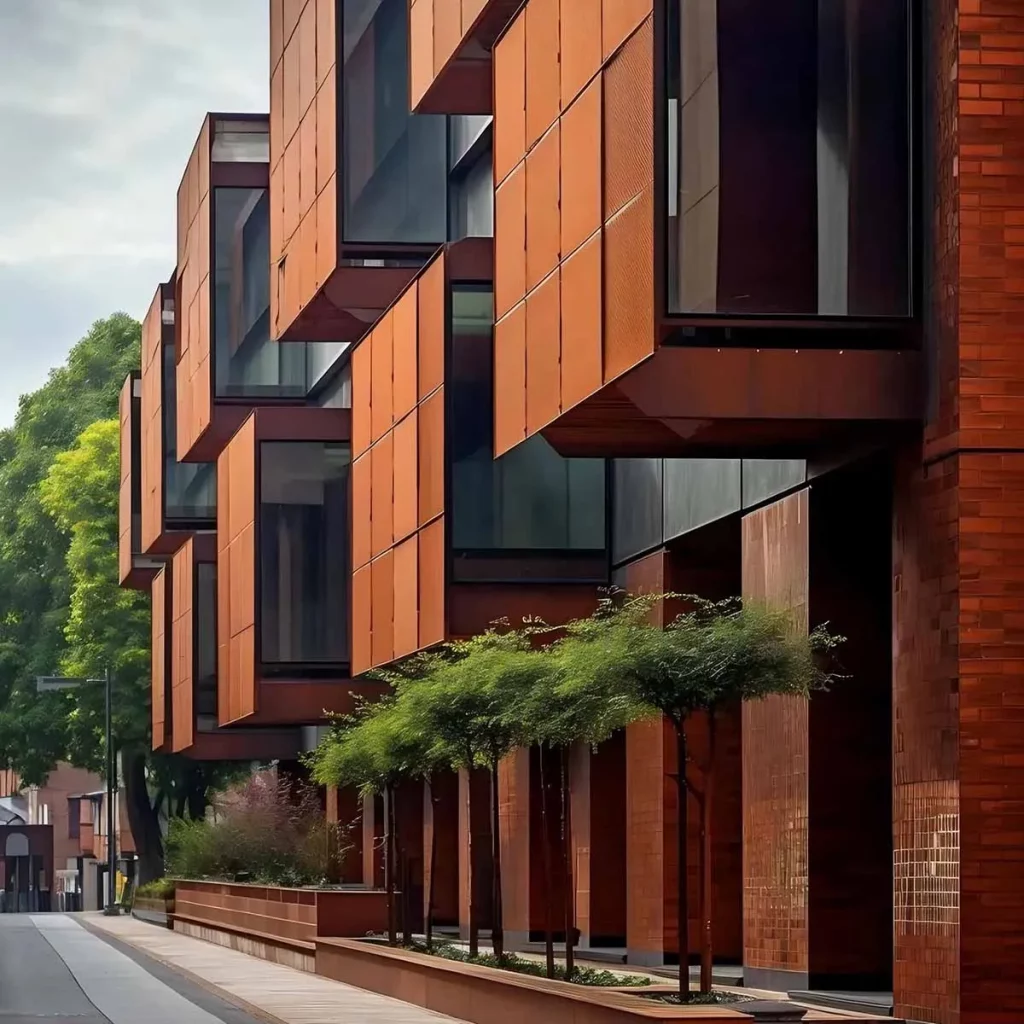
In conclusion, corrugated corten steel panels present a compelling solution for a multitude of applications. Their combination of durability, aesthetic versatility, and cost-effectiveness makes them an attractive choice for both large-scale projects and intricate designs. Understanding the various manufacturing processes, installation techniques, and design considerations allows for informed decisions when integrating these panels into projects, leading to aesthetically pleasing and functionally sound results. The versatility of these panels opens up new possibilities in both construction and design.