Milsap Retaining Wall Design & Construction
Milsap retaining walls offer a strong solution for various landscape projects. This comprehensive guide explores the design considerations, construction methods, geotechnical aspects, and long-term maintenance for these structures. Understanding the different materials, soil conditions, and potential issues is key to ensuring a durable and stable wall.
From selecting the right material – whether concrete, steel, or composite – to navigating site-specific challenges like soil conditions and topography, this discussion provides practical insights into each step of the process. A deep dive into the crucial geotechnical considerations, including soil testing and drainage systems, will ensure a solid foundation for the retaining wall’s longevity.
Construction Methods and Procedures: Milsap Retaining Wall
Milsap retaining walls, known for their robust design and adaptability, require meticulous construction to ensure structural integrity and longevity. Proper execution of each step, from site preparation to final inspection, is critical for a successful project. Careful consideration of safety measures and the selection of appropriate equipment further enhances the efficiency and quality of the construction process.
Site preparation is paramount for a stable and successful Milsap retaining wall. This involves accurate surveying, clearing the site of obstructions, and establishing precise grade lines. Precise excavation, formwork, and reinforcement are essential to ensure the structural integrity of the wall.
Site Preparation and Excavation
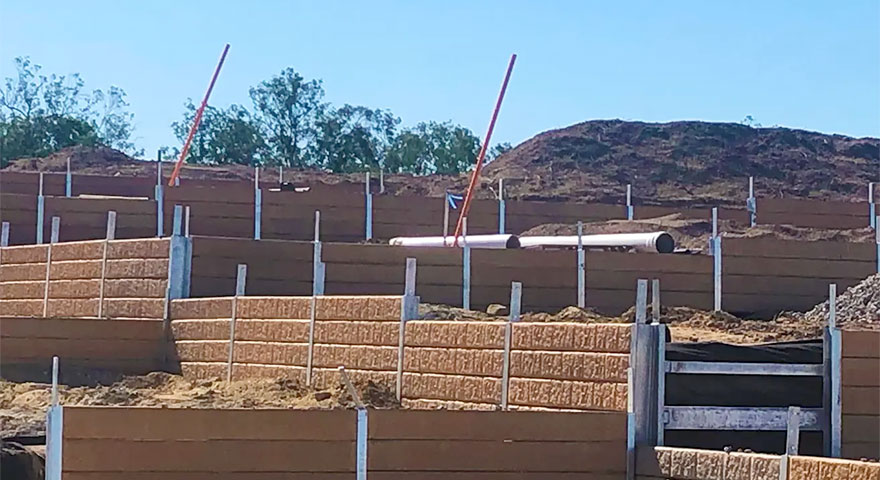
Thorough site preparation minimizes potential issues during construction. This includes removing vegetation, debris, and unsuitable soil to ensure a solid foundation. Precise surveying and marking of the retaining wall’s footprint are critical for accurate placement. Appropriate soil testing determines the bearing capacity of the soil and informs the excavation design. Different excavation methods are employed based on site conditions and the scale of the project.
- Precise Surveying and Marking: Using surveying equipment like total stations and laser levels, the design specifications for the retaining wall are accurately transferred to the site. This ensures the wall is constructed to the correct dimensions and grade. Proper marking of the wall’s footprint, using stakes and string lines, prevents errors during excavation and subsequent construction phases.
- Clearing and Grubbing: Removal of vegetation, roots, and debris is vital to prevent future issues and ensure a stable foundation. Careful consideration of tree roots, as well as rock and other obstructions, must be taken into account during this stage.
- Soil Testing: Soil samples are taken to determine the soil’s bearing capacity and suitability for the retaining wall. This testing informs the design and construction methods, especially regarding the selection of appropriate backfill materials and the design of the foundation.
- Excavation Methods: Various excavation methods can be employed depending on the soil type, the wall’s dimensions, and the overall project constraints. Examples include manual excavation with shovels and backhoes, mechanical excavation with excavators, and trenching methods for smaller walls. The choice of method is critical to ensure that the excavation process is both safe and efficient.
Formwork and Reinforcement
Formwork provides the temporary structure that shapes the wall’s concrete elements. Reinforcement, typically steel rebar, enhances the wall’s tensile strength and resistance to bending forces. The design of the formwork and the placement of reinforcement are critical to ensure the wall’s long-term stability and durability.
- Formwork Design: Formwork is constructed according to the design specifications, ensuring the precise dimensions and shape of the wall. The formwork needs to be rigid and stable enough to resist the pressure of the concrete during pouring and curing. Types of formwork include plywood, steel, or composite materials, each with its advantages and disadvantages.
- Reinforcement Placement: Steel rebar, strategically placed within the concrete, strengthens the wall against bending and tensile stresses. The placement of the rebar is critical to ensure its proper distribution throughout the concrete. Reinforcement placement must be according to the engineering design and building codes.
Concrete Placement and Curing, Milsap retaining wall
Proper concrete placement and curing are crucial to achieving a strong and durable wall. This involves using appropriate concrete mix designs, ensuring proper vibration, and maintaining the required curing conditions. The concrete’s quality and consistency directly affect the wall’s structural integrity.
- Concrete Mix Design: The specific mix design for the concrete is chosen based on factors such as the soil type, the expected loads, and the environmental conditions. Different concrete mix proportions are used for different applications, such as those involving high-strength concrete or for specific weather conditions.
- Vibration and Compaction: Adequate vibration and compaction are essential to ensure the concrete fills all the forms and voids, eliminating air pockets. This process ensures the concrete is dense and uniform, leading to a strong wall.
- Curing Procedures: Proper curing procedures are crucial to allow the concrete to gain its full strength and durability. This involves maintaining the proper moisture content and temperature for a specified period. This often involves covering the concrete with wet burlap or plastic sheets to maintain moisture.
Final Inspection and Backfilling
Final inspection ensures the wall meets all design specifications and quality control standards. Backfilling is completed with compacted soil, ensuring stability and drainage. The final inspection and backfilling are essential steps in ensuring a successful and durable project.
- Final Inspection: A final inspection verifies that the completed retaining wall adheres to all design specifications and local building codes. This involves checking for proper dimensions, reinforcement placement, and concrete quality. Inspectors assess the overall structural integrity and ensure the wall is ready for use.
- Backfilling and Compaction: Backfilling the area behind the retaining wall with compacted soil is a crucial step to provide stability and prevent future settlement. The soil is compacted using specialized equipment to ensure its density and prevent future issues.
Geotechnical Considerations
Source: dfwpoolretainingwalls.com
Proper geotechnical analysis is crucial for the successful design and construction of Milsap retaining walls. Understanding the soil properties, potential for instability, and drainage requirements directly impacts the wall’s long-term performance and safety. Ignoring these factors can lead to costly repairs, structural failure, or even hazards to surrounding areas.
Soil conditions significantly influence the design parameters of a retaining wall. Factors such as soil type, density, moisture content, and the presence of any potential weak layers must be considered. A comprehensive understanding of these elements is vital for designing a stable and enduring retaining wall.
Importance of Soil Testing and Analysis
Soil testing and analysis are essential to determine the physical and mechanical properties of the soil. These properties directly influence the bearing capacity, settlement potential, and stability of the retaining wall. Thorough laboratory testing provides crucial data for accurate calculations and ensures the design meets the necessary safety standards. This includes testing for shear strength, compaction characteristics, and permeability. Different testing methods like direct shear tests, triaxial tests, and consolidation tests are employed to assess these parameters.
Different Types of Soil Conditions
Various soil types exhibit different characteristics that impact retaining wall stability. Understanding these differences is critical for effective design.
- Clay soils tend to exhibit low bearing capacities and are susceptible to significant volume changes with moisture fluctuations. These changes can cause settlement and affect the stability of the wall. Proper drainage systems are crucial to mitigate these effects.
- Sandy soils, conversely, generally have higher bearing capacities and better drainage characteristics. However, loose sand can be prone to settlement and liquefaction under seismic activity, requiring careful consideration in the design process.
- Gravelly soils typically possess high bearing capacities and good drainage. Their inherent stability makes them suitable for a wide range of retaining wall applications, but the presence of large stones or boulders may require special handling procedures during construction.
Role of Geotextiles and Drainage Systems
Geotextiles and drainage systems play a critical role in improving the stability and longevity of Milsap retaining walls. These systems manage water flow, prevent soil erosion, and ensure the stability of the soil mass behind the wall.
- Geotextiles, often placed between the wall and the soil, act as a filter, preventing soil particles from clogging the drainage system. This ensures the system’s long-term effectiveness.
- Properly designed drainage systems facilitate the removal of water from behind the wall. This is particularly important in areas with high rainfall or groundwater levels. Excessive water pressure can destabilize the soil and the retaining wall itself.
Assessing Slope Instability and Settlement
Assessing the potential for slope instability or settlement is a critical aspect of the geotechnical analysis. Careful consideration must be given to the topography, the geological conditions, and the potential for future changes.
- Geological surveys and site investigations help identify potential weaknesses in the soil strata and geological formations, providing a clear picture of the site conditions.
- Analyzing existing slopes in the vicinity can provide valuable insights into potential failure mechanisms and settlement patterns. Previous cases of slope failures or settlements in similar soil conditions can offer guidance for the design.
Soil Bearing Capacities for Milsap Retaining Walls
The table below provides a general guideline for the typical bearing capacities of different soil types. Actual values may vary significantly depending on the specific site conditions and soil characteristics.
Soil Type | Bearing Capacity (kPa) | Typical Applications |
---|---|---|
Clay | Low to Moderate | Gentle slopes, moderate loads |
Sand | Moderate to High | Steep slopes, high loads |
Gravel | High | Steep slopes, high loads |
Maintenance and Repair
Proper maintenance and repair strategies are crucial for the longevity and structural integrity of Milsap retaining walls. Regular inspections and timely interventions can prevent costly repairs and ensure the wall continues to function as intended. Addressing potential issues proactively is key to avoiding significant damage and ensuring the safety of surrounding areas.
Long-Term Maintenance Requirements
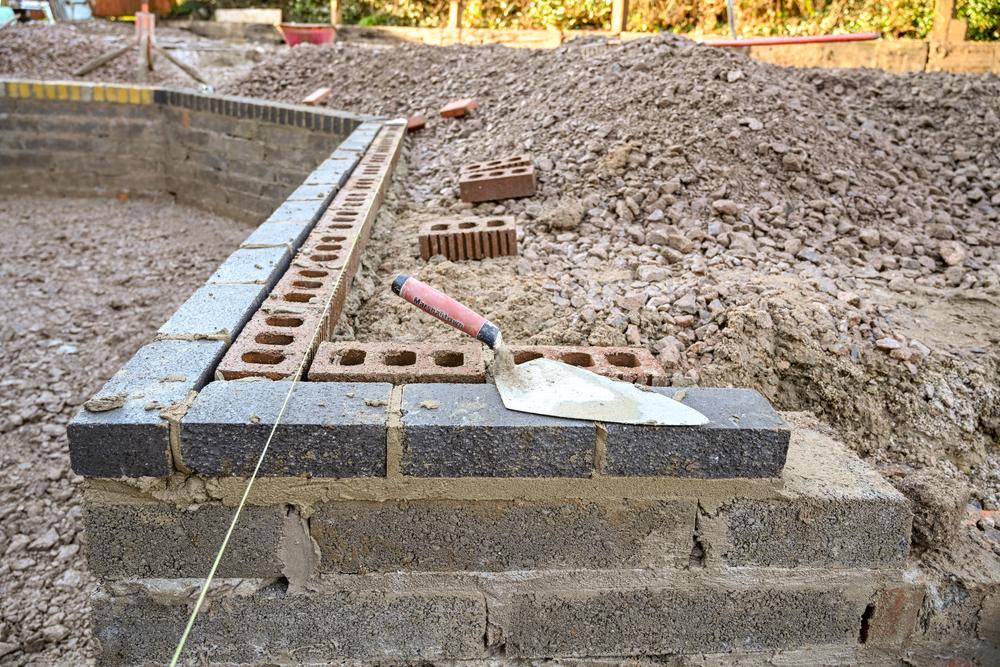
Maintaining the structural integrity of Milsap retaining walls requires a proactive approach. Regular inspections are essential for identifying potential problems early, allowing for prompt repairs before they escalate into significant issues. This involves a combination of visual inspections, monitoring of soil conditions around the wall, and periodic assessments of drainage systems. Preventing water infiltration and maintaining good drainage is paramount to preventing deterioration. Furthermore, monitoring for signs of settlement, cracking, or bulging is essential.
Common Issues and Solutions
Several issues can affect Milsap retaining walls over time. Water infiltration, often due to inadequate drainage, is a significant concern. Solutions include improving drainage systems, installing weep holes, and sealing cracks to prevent water penetration. Soil erosion around the base of the wall can destabilize the structure. Addressing this involves reinforcing the soil with geotextiles or other appropriate measures and maintaining adequate landscaping around the base to prevent erosion. Differential settlement of the supporting ground can also cause issues; careful site preparation and ground stabilization measures can mitigate these risks.
Repair Techniques for Damaged Walls
Repair techniques for damaged Milsap retaining walls depend on the specific nature of the damage. For minor cracks, epoxy injections or crack fillers can be effective. More extensive damage might require underpinning, which involves supporting the wall with additional foundations. Improving the surrounding soil to improve drainage and stability can be part of the repair process. In cases of significant structural failure, complete reconstruction might be necessary. Using appropriate reinforcement materials and techniques can strengthen the wall and improve its resilience against future damage.
Importance of Regular Inspections and Preventive Maintenance
Regular inspections and preventative maintenance are crucial to mitigate risks associated with Milsap retaining walls. Regular visual inspections allow for the early detection of potential issues, preventing small problems from escalating into major structural failures. Addressing minor issues promptly avoids costly repairs and ensures the longevity of the wall. Inspecting drainage systems, monitoring soil conditions, and checking for signs of settlement or movement can significantly reduce the need for extensive repairs in the future. A proactive approach to maintenance is always more economical and efficient than reactive repair efforts.
Identifying Potential Issues Through Visual Inspection
Visual inspection is a critical tool for identifying potential issues with Milsap retaining walls. Key indicators include cracks or signs of movement in the wall itself, settlement of the surrounding soil, or excessive water accumulation around the base. Bulging or leaning of the wall structure also signals a potential problem. Checking for vegetation growth, which could be an indication of soil erosion, is also essential. The presence of excessive moisture or standing water in the area surrounding the wall can suggest issues with drainage. Careful attention to these visual cues can help in identifying potential problems early, enabling timely interventions.
Last Point
Source: dfwpoolretainingwalls.com
In conclusion, constructing a successful Milsap retaining wall requires careful consideration of design elements, construction procedures, and geotechnical factors. The choice of materials, the site’s conditions, and appropriate safety measures are all critical to the wall’s long-term performance. Regular maintenance and proactive identification of potential issues further enhance the wall’s lifespan and ensure its stability. This detailed guide provides a framework for successful projects, enabling informed decision-making at each stage.